
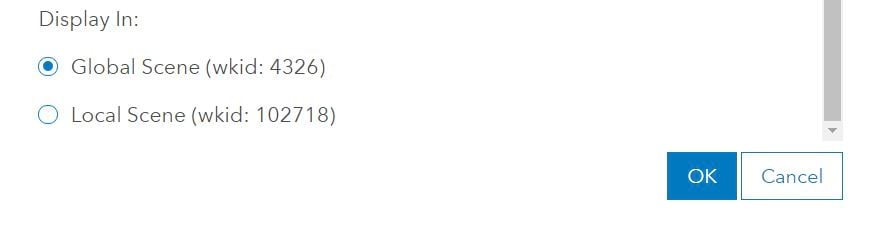
Numerical and experimental studies are conducted to illustrate the effectiveness of the proposed method. Then, optimization problems involving cross-infill angles as design variables are formulated, including concurrent optimization formulation. Numerical homogenization is performed to evaluate the equivalent effective properties of the 100-percentage cross-infilled local microstructures, and by introducing fitting functions, the relationship between equivalent effective material properties and varying cross-infill angles is empirically constructed. This method features in modeling the process-induced material anisotropy through microscopic geometric modeling obtained by scanning electron micrographs. This paper contributes a concurrent topological structure and cross-infill angle optimization method for material extrusion type additive manufacturing (AM). Several numerical examples were investigated to verify the effectiveness of the proposed method, while satisfactory optimization results have been derived. An asynchronous starting strategy is proposed to prevent the local minimum solutions caused by the concurrent optimization scheme. With this setup, a concurrent optimization problem was formulated to simultaneously optimize the topological structure of the printing layer, the multipatch distribution, and the corresponding deposition directions.
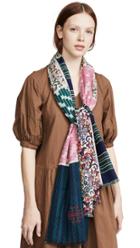
The level set method was employed to represent and track the layer shape evolution discrete material optimization (DMO) model was adopted to realize the material property interpolation among the patches. The 'multipatch' concept consists of each printing layer disintegrated into multiple patches with different zigzag-type filament deposition directions. Abstract: This paper presents a hybrid topology optimization method for multipatch fused deposition modeling (FDM) 3D printing to address the process-induced material anisotropy. Featured Application: This work can be used for lightweight design of drone structures.
